Строительство трубопроводов, антенн, мостов, производство зубчатых колес, станин, шкивов, коленвалов, турбинных дисков и лопаток, а также комплектующих для авиационной отрасли и других изделий требует сверхнадежного соединения металлических и некоторых неметаллических элементов. Такие соединения выполняются методом сварки, что обеспечивает их высокую надежность, но только в случае, если сварные швы выполнены качественно.
Сварные швы: определение, процесс образования и структура
Сварные швы представляют собой соединение краев элементов, которые под воздействием сварочного аппарата превращаются в единую, неразъемную конструкцию. Это происходит благодаря кристаллизации расплавленного материала, его пластической деформации под высоким давлением или сочетанию этих процессов.
С точки зрения структуры, сварные швы состоят из основного и присадочного металлов (или полимеров, композитов), которые в процессе сварки сливаются и образуют сплав, представляющий собой более-менее однородную субстанцию. Эти материалы соседствуют с узкой зоной сплавления, где происходит кристаллизация расплавленных частиц обоих материалов, а далее – с зоной термического воздействия. Последняя фактически является основным металлом, несколько поменявшим структуру и свойства при смене температур, но полностью сохранившим химический состав. Зона термического воздействия определяется по светлым оттенкам, в то время как шов имеет более темный цвет.
Структуру сварных соединений можно рассматривать и с геометрической точки зрения. В поперечном сечении они состоят из следующих элементов:
- корня шва;
- провара (проплавления);
- толщины шва;
- лицевой поверхности;
- границы наружной поверхности;
- усиления.
Для стыковых соединений также важно учитывать провар корня, а для угловых соединений — катет шва. Помимо основных элементов, в конструкции сварных швов могут быть дополнительные элементы, которые зависят от типа соединения. Все параметры регулируются ГОСТом 2601-84.
Типы сварных швов
Сварочным аппаратом чаще всего выполняются соединения различных металлических изделий, таких как пластины, уголки, швеллеры, трубы, квадраты и другие элементы проката. Взаимное расположение этих деталей служит основой для классификации сварных швов. К наиболее распространённым типам относятся:
- Стыковые швы — выполняются между торцами изделий, расположенных в одной плоскости.
- Нахлёсточные швы — соединяют параллельно расположенные элементы, края которых частично накрывают друг друга.
- Угловые швы — образуются в месте соприкосновения заготовок, размещённых под углом.
- Торцовые швы — позволяют соединить края изделий, наложенные друг на друга.
- Тавровые швы — подразумевают соединение торца одной заготовки с плоскостью другой.
Эти типы могут делиться на подвиды в зависимости от формы кромок соединяемых деталей — ровные, скошенные или криволинейные. Классификация также зависит от назначения, длины, конфигурации, типа свариваемых материалов, положения в пространстве, количества проходов, а также от действующего усилия и других характеристик.
Подробные характеристики всех типов сварных швов можно найти в ГОСТах Р ИСО 17659–2009, 5264–80, 14771–76, 14806–80, 14776–79, 16037–80, 15164–78, 15878–79 и других. В этих документах также описаны технологии их выполнения.
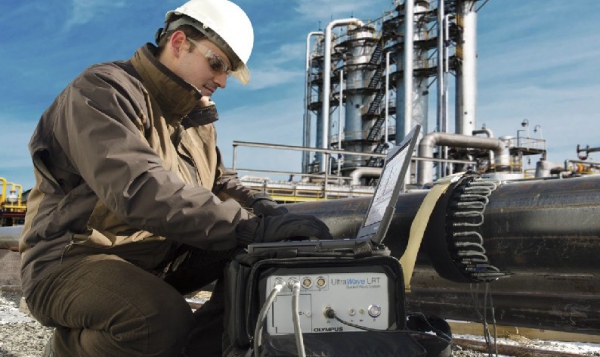
Обеспечение качества сварных швов
Основными показателями качества сварных швов являются прочность и несущая способность. Обеспечение этих характеристик начинается на стадии проектирования изделия, где согласовываются геометрия швов, тип сварки, вид разделки кромок и допустимые отклонения от стандартов, установленных ГОСТами.
Следующий этап включает подготовку материалов. Для тонких деталей (до 1 мм) выполняется механическая и химическая зачистка поверхностей. Для заготовок толщиной 1–4 мм необходимо дополнительно выполнить отбортовку — прокатку торцов на специальном оборудовании с целью их утончения. Если толщина заготовки превышает 4 мм, проводят притупление и скашивание кромок.
Особое внимание уделяется разделке кромок, так как она обеспечивает правильный доступ электрода к корню шва, уменьшает площадь поперечного сечения и снижает внутренние напряжения, возникающие после кристаллизации материала. В зависимости от типа сварки разделка может быть одно- или двусторонней, а её форма зависит от типа соединения. Это может быть Х-, V-, U-образная, уступчатая или криволинейная форма.
После тщательной подготовки детали свариваются, и полученный шов очищается от технологических загрязнений, таких как шлак, окалины или брызги материала. На этом этапе также проводится контроль качества соединений, который позволяет выявить дефекты и определить оптимальные способы их устранения.
Наиболее эффективные способы контроля сварных швов и оборудование для их реализации
Контроль сварных швов регулируется ГОСТ 3242–79, который описывает неразрушающие методы как наиболее целесообразные для проверки качества соединений. К таким методам относятся технический осмотр, а также радиационная, магнитная и капиллярная дефектоскопия. Одним из таких методов является акустический способ обнаружения дефектов, который описан в ГОСТ Р 55724-2013. Этот метод основан на принципах движения и отражения ультразвуковых волн и имеет несколько ключевых преимуществ.
Во-первых, ультразвуковой контроль сварных швов (УЗК) позволяет обнаруживать все виды дефектов, включая те, которые могли быть незамечены при визуальной проверке, такие как поверхностные поры, трещины, наплывы, подрезы, а также внутренние дефекты — непровары, несплавления, флюсовые включения. Во-вторых, ультразвуковая диагностика позволяет контролировать качество соединений толщиной до 10 мм, а также выявлять сквозные дефекты в трубопроводах высокого давления (ГОСТ 16037).
Ультразвук используется не только в лабораторных условиях, но и непосредственно на производстве. Для этого предлагаются портативные дефектоскопы, которые отличаются высокой чувствительностью, широким спектром измерений и точностью. Благодаря этим устройствам контроль сварных швов на трубах, ёмкостях и других продуктах осуществляется быстро и эффективно.
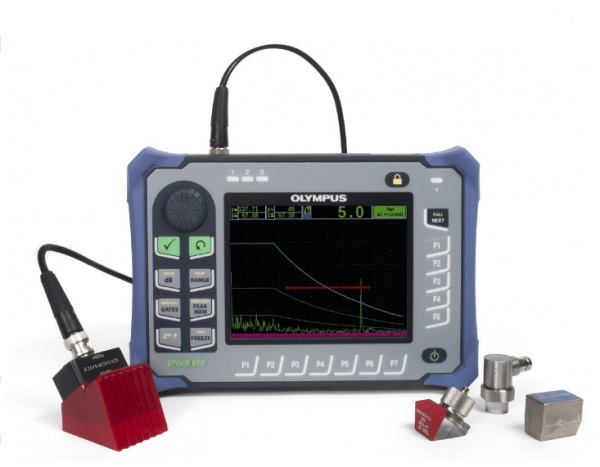